Digital Manufacturing and Surface Engineering (DMS)
The DMS Research Group performs internationally recognized research in the field of digital manufacturing and surface engineering.
The group is co-lead by Prof. Antti Salminen and Prof. Ashish Ganvir.
Some of the topics that are covered under the broad umbrella of DMS are for examples:
- Digital materials (metals, ceramics, polymers and composites) processing using laser, plasma, combustion flames, electron-beam etc.;
- Digital robotized liquid (solution precursors, suspensions etc.) and solid (wire as well as powder) processing,
- Digital joining (e.g. welding) & 3D printing of materials
- Digital surface engineering: thin and thick films, tribology and corrosion of surfaces, modern thermal spray techniques, surface modification by thermal and mechanical means
- Process monitoring, modeling and simulations.
DMS as a newly established research group has renowned young and experienced experts working in the above-mentioned fields with combined industrial and academic experience of well over 50 years. The group´s ambition is to conduct applied industrially relevant yet fundamental scientifically driven research and development. Some of the target applications for DMS are biomedical, automotive, power generation, aerospace, space, marine, renewable energy and many more.
As of November 2023, the group has over 25 members working directly within the group or associated with it from other groups or other organizations. The group consists of several professors, adjunct professors, guest scientist, postdoctoral scientists, PhD/doctoral candidates, junior researchers (research assistants, interns etc.) and research engineers.
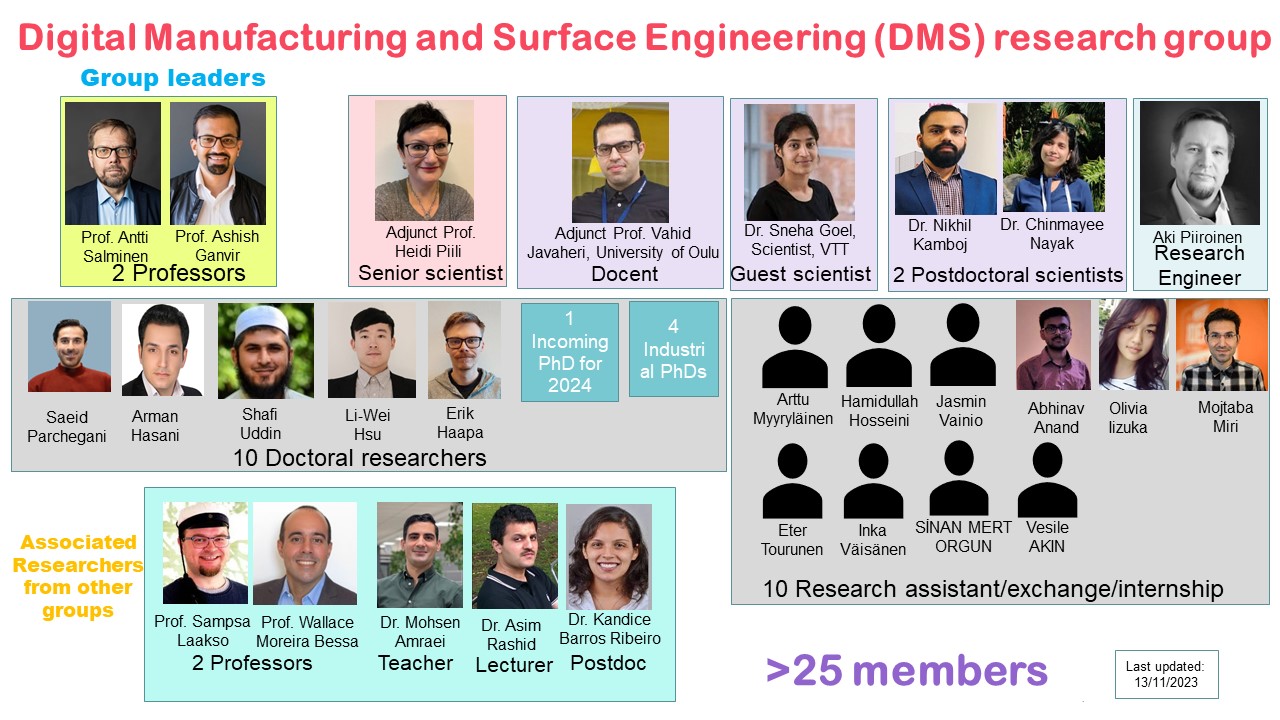
We are constantly growing and recruiting more researchers, especially post-docs, PhD students and MSc thesis students. Interested candidates who wish to apply for fellowships and work in our group are most welcome to contact us.
DMS infrastructure and facilities
Our DMS lab is very well equipped with advanced infrastructure required for conducting highly scientific as well as applied research activities within the field of digital manufacturing and surface engineering. DMS infrastructure is located in a collaborative facility called as “Machine Technology Centre (MTC)”. At MTC, the DMS lab is equipped with several digital manufacturing and surface engineering related facilities. For example, several additive manufacturing or 3D-printing machines, surface degradation testing such as corrosion and tribology, process monitoring sensors etc. DMS lab has strong ties with other units at UTU to access various materials testing and characterization tools such as electron and optical microscopes, X-ray diffraction, mechanical testing, feedstock (powder and liquid) characterization etc. Moreover, the researchers in DMS have strong collaboration with European large-scale infrastructure facilities (e.g. Paul Scherrer Institute (PSI), Switzerland) to conduct advanced analysis of digitally manufactured or surface engineered materials using synchrotron and neutrons.
Powder bed fusion additive processes @DMS
The latest addition to DMS has been this modular open access laser powder bed fusion 3D-printer that is capable of printing single and multi-materials. It has two build platforms, one with Diameter 250 mm and other with diameter 50 mm. Small build platform allows development of expensive materials with less cost.
DMS is collaborting with Turku University of Applied Science to use shared two SLM 280 machines placed at MTC.
Direct energy deposition additive and coating processes @DMS
DMS is equipped with several industrial robots, laser and arc heat source, powder and wire feeders, and nozzles which can be used for 3D-printing, welding as well as coating and surface modifications.
- Laser wire
- Laser powder
- Arc wire
- Thermal Spray Facility (To be commissioned in Autumn 2024)
- High power 10 kW multimode fiber
- 3kW
- 2kW SM fiber
- 100W SM pulsed ns fiber laser
Other Lasers and related process capabilities @DMS
- IPG-YLS 10000 MM with four fiber outputs (10 kW multimode fiber laser)
- IPG-YLS 2000 SM, 2kW SM fiber + Arges Elphant 3D Scanner optics (400 x 400 mm work area) / For remote laser welding
- YLPN-1-20x120-100 Pulsed ns fiber laser (20-120 ns / 0.13 – 1.0 mJ) + IPG mid power scanner optics (170 x 170 mm work area) / For laser marking
- Bodor 3kW fiber laser cutting machine
- Precitec YW52 Welding opitcs
- Precitec YC52 Cladding optics + GTV powder feeder
- Precitec YRC cutting optics for robot laser cutting
- IPG D50 Wobble welding head (2D scanner mirrors) + LDD700 Inline coherent imaging systems (Sensor has own 2D scanner)
- Cavitar C300 Welding Camera:
- Xarion Eta250 Ultra sensor optical ultrasonic microphone: This optical microphone is used to monitor various phenomena relevant during processing and testing of material( e.g. crack formation, microstructure change, etc.) using acoustic airborn sensor. The Eta250 Ultra sensor is the optical microphone for monitoring applications, in combination with a powerful data acquisition system such as the HFMES. The optical microphone can be combined with your own DAQ as well though, as it simply provides an analog signal of +- 15 V (10 Hz – 1 MHz).
Surface engineering testing capabilities @DMS
The modular POD-4.0 is a tribometer with many capabilities. Use it as a pin/ball on disk for rotary tests, linear reciprocation or traction measurement simply by choosing the right module. Take advantage of its automation, sensitivity and ultrawide range of operation. The current setup at UTU has Rotary Module and is compatible with Materials like, Superalloys, thermally sprayed, laser cladded coatings (metals, cermets, and ceramic) as well as additively manufactured bulk components (metals, ceramics and cermets). More specifications are as follows:
- Load: 2 to 200 N (manual load)
- Speed: 1 to 2000 rpm (variable, computer controlled, high precision A)
- Angular reciprocation: 0.3 to 5 Hz
- Friction: 0 to 100 N (high resolution A)
- Linear wear: 0 to 2 mm
- Sensors: Humidity (< 95%) and Temperature ( -40 to 250 deg C)
- Wear Track Diameter: 5 to 40 mm (computer controlled)
- Bottom specimen holder: 20 to 40 mm (dia), thickness of 10 mm
- Pin or Ball Holder: 6 mm (dia)
- Tribocorrosion module
The biotribometer is compatible with various types of Biomaterials including ceramics (hydroxyapatite, Zirconia, etc.) coatings and additively manufactured implants (steel, Ti64, Zirconia etc.) The triobometer can measure wear as well as friction under simulated body fluid conditions. More specifications are as follows:
- ASTM F732 Compatible
- Customizable Load Profiles
- Customizable Wear Profiles
- Load range: 10 to 600 N (computer controlled)
- Friction range: 0 to 100 N
- Linear wear: 0 to 2 mm
- Reciprocation: X, Y = 3 to 30 mm, f = 0.5 to 5 Hz
- Elliptical: X = 3 mm, Y = 13 mm, f = 1 Hz
- Circular: 2 to 10 rpm
- Lubricant cup: 50 ml
- Lubricant heating: RT to 70 deg C
- Bottom specimen holder: 30 mm (dia) x 10 mm (thickness), Other size is possible
- Pin or Ball Holder: 6 mm (dia)
The Vertex.100mA.EIS is a versatile entry-level potentiostat which has ±100mA / ±10V compliance and integrated impedance analyser up to 1MHz. This can be used as Potentiostat, Galvanostat, Impedance Analyser and Electrometer. The equipment is compatible with measurement Techniques such as corrosion measurement & analysis, Electrochemical Impedance Spectroscopy, Electroanalytical Voltammetry techniques, Pulse Voltammetry Techniques, Chrono techniques, Coulometry, Bio-sensing, Electro-deposition, Electro plating, Battery/ Fuel cell, Supercap testing, Solar cell testing, Spectro/ Nano-electrochemical testing etc. More specifications are as follows:
- Number of channels in instrument: 1
- Current compliance: ±100mA
- Maximum compliance voltage: ±10V
- Maximum applied voltage: ±10V
- Electrode connections: 4; WE, CE, RE, S (and GND) with 4mm banana plugs
- Potentiostat bandwidth: >500kHz
- Stability settings: High Speed, Standard and High Stability
- Programmable response filter: 1MHz, 100kHz, 10kHz, 1kHz, 10Hz
- Signal acquisition: Dual channel 16bit ADC, 100,000 samples/s
The Micro-Scale Abrasion Tester is based on an experimental technique that can be used to determine the wear coefficient of hard and soft coatings and monolithic materials by abrasive wear in a ball on plate contact configuration. The machine may also be used as a crater-generating tool on coated surfaces for coating thickness determination. The equipment may be used for tests in accordance with BS EN 1071-6: 2007: Advanced technical ceramics. Methods of test for ceramic coatings. Determination of the abrasion resistance of coatings by a micro-abrasion wear test. The application of this equipment can be for example measurement of abrasion resistance, abrasive wear, ball cratering test, brittle materials, coatings, dental materials, micro-scale abrasion, paint films, slurry abrasion, three body abrasion, wear by hard particles. More specifications are as follows:
- Ball Speed Range: 30 to 150 rpm
- Load Range: 0.05 to 5 N
- Ball Diameter: 25 mm
- Pump Feed Rate: up to 60 ml/hour
DMS Research Projects
Gold mining is very expensive industry and therefore opportunities resulting in low cost gold production are needed, which is spurring the utilization of tailings as well as other secondary resources. Gold is also one of the most wasteful metals where almost 99% ends up as waste and produced tailings are causing huge environmental risks. Therefore, it would be extremely important to enhance the gold recovery from the secondary resources. In this project, novel electrochemical reactors are constructed by using additive manufacturing (AM) and investigated for electrochemical production of chlorine for efficient gold leaching from the solid residues followed by its selective recovery. Especially, closed-loop gold recovery with zero emissions will be obtained. Additive manufacturing provides novel manufacturing method of very complex shapes and geometries, thus enabling manufacturing of totally new design of electrodes by requirements of targeted applications. This freedom in design of electrodes can remarkably enhance efficiency of electrochemical reactors. At the same time, important knowhow via monitoring related to the additive manufacturing of electrodes with versatile and complex geometries from different materials will be achieved. Electro-efficiency of the recovery systems is maximized in order to increase the sustainability of the novel processes.
The ReGold-AM project (2019 - 2023) is funded by Academy of Finland. The PI in University of Turku is Docent Heidi Piili and the project is carried out in tight cooperation with Professor Eveliina Repo from LUT university (LUTSepPur). Project is carried out with national and international collaborators from both academy and industrial sectors.
The GREEN-BAT project is aiming to bring a technological innovation in the field of solid-state-batteries by proposing a novel manufacturing route to produce individual all-solid-state-lithium-batteries (ASSLB) constituents and subsequently explore sequential processing for their facile consolidation into full ASSLB cell; using direct multi-material processing technologies in lieu of the current state-of-the-art ASSLB several-step manufacturing route where different manufacturing technologies are used to produce different ASSLB constituents (current collectors, electrodes and electrolyte). Successful realization of GREEN-BAT will have a significant impact on the ASSLB market serving several industrial sectors, especially transport.
GREEN-BAT project (2022–2025) is funded under M-ERA.NET 2021 which is an EU-funded international network. From Finland the funding organization is Academy of Finland. University of Turku is coordinating this project and the consortium project partners across Europe are University West, Sweden; Fraunhofer IWS, Germany; LiFeSiZE AB, Sweden. Prof. Ashish Ganvir is the project coordinator and PI from University of Turku.
The additive manufacturing techniques get higher interest of the material scientists all over the world. The unique possibilities of printing the complex shapes and tailoring the microstructure and mechanical properties have a great potential for real life applications. This project is focusing on tailoring the microstructure of novel Fe-based alloy by manipulating the processing conditions. Subsequently the project is aiming to gain an in-depth understanding about the deformation behaviour of the 3D printed material and its correlation with the manipulated microstructure. Successful execution of this project will add a new alloy into the list of novel materials for 3D printing using powder bed fusion.
The PI from University of Turku is Prof. Ashish Ganvir and the project is executed in collaboration with Paul Scherrer Institute (PSI), Switzerland.
Additive manufacturing (AM) is a manufacturing technology of which popularity has risen last years. Today, AM is used for manufacturing of demanding components and in serial production, and not just for manufacturing of single series components, like prototypes and visual models. In the DREAMS project, a comprehensive material database will be created. A considerable number of test specimens will be AMed by service providers and research institutes, and analysed in-depth by research institutes. This material database can be utilized in certification of critical components used in e.g., aviation, oil & gas, and nuclear industries. The material database is a must for engineering the critical components for additive manufacturing and certification. Another tangible example of results of this project is the fully determined quality pyramid in which the five quality levels for AMed components are defined.
DREAMS project (2022–2024) is funded under Business Finland. Prof. Antti Salminen is PI of the project on University of Turku's side. The consortium project partners in Finland are University of Oulu, Lappeenranta-Lahti University of Technology LUT and FAME 3d ecosystem, with large number of Finnish industries. The international collaboration in project is planned with Fraunhofer IPK, Germany, Penn State University, U.S.A. and Paul Scherrer Institute, Switzerland.
The Hit and Sink project will develop a new type of virtual reality-based training method for companies offering and using 3D printing to improve their competitiveness. The content of the training is planned in cooperation with Finnish companies. 3D printing is already used quite widely in the world and the growth in use is anticipated to continue to be strong. Goal is to develop a new method of training and familiarization, the implementation of which utilizes the 360/virtual reality environment. The Hit and Sink training method is a 360-VR technology-based model that supports dialogue, case specificity and micro-learning. The material will contain extensive information about 3D printing, both in terms of theory and practice. It is intended that training material can be integrated into the continuous development of staff to promote the competitiveness of enterprises. The new training method can also be used in the future to promote the use of other new technologies.
Hit and Sink project (2021–2023) is funded by European Social Fund within REACT-EU. The project PI in Mechanical Engineering is Professor Antti Salminen and project is carried out in collaboration with Turku School of Economics at University of Turku. The project is collaborating with 10 local companies.
The project aims to develop know-how and technical preparedness in higher education institutes as well as in industrial companies by development of additive manufacturing of metals.
The additive manufacturing techniques get higher interest of the material scientists all over the world. The unique possibilities of printing the complex shapes and tailoring the microstructure and mechanical properties have a great potential for real life applications. This project is continuation of previous DEFAMe project. In this project we will use neutron diffraction to gain an in-depth understanding about the deformation behaviour of the 3D printed material and its correlation with the manipulated microstructure. Successful execution of this project will add a new alloy into the list of novel materials for 3D printing using powder bed fusion. The PI from UTU is Prof. Ashish Ganvir and the project is executed in collaboration with Paul Scherrer Institute (PSI), Switzerland.
The project aims to study 3D printed and plasma sprayed solid state batteries and study the solid-solid interfaces of as-sprayed and laser glazed plasma sprayed solid state batteries using large scale synchrotron facilities. The PI from UTU is Prof. Ashish Ganvir and the project is executed in collaboration with Paul Scherrer Institute (PSI), Switzerland, University West, Trollhättan, Sweden and ETH Zurich, Switzerland.
In this project we are developing LPBF process to 3D-print multi-material specimens and study their interfacial characteristics via operando LPBF experiments together with large scale Synchrotron facilities. The PI from UTU is Dr. Sneha Goel and the project is executed in collaboration with Paul Scherrer Institute (PSI), Switzerland.
The project aims to laser glaze the plasma sprayed solid state batteries and study the solid-solid interfaces of as-sprayed and laser glazed plasma sprayed solid state batteries using large scale synchrotron facilities. The PI from UTU is Prof. Ashish Ganvir and the project is executed in collaboration with Paul Scherrer Institute (PSI), Switzerland, University West, Trollhättan, Sweden and ETH Zurich, Switzerland.
Digital Manufacturing and Surface Engineering (DMS) coordinates the Manufacturing Research Survey (EMS) on behalf of Finland as a part of the EU-formed consortium. EMS Finland forms a research alliance between 21 EU states. The research is coordinated in the Fraunhofer Institute for Systems and Innovation Research (ISI). EMS research group aims to promote scientific knowledge in the manufacturing sector. In the future, the research group’s activities will include close government-leading project work with the business community and Horizon Europe projects. The projects focus on assessing the manufacturing industry in practical requirements. Accordingly, we will explore how universities should educate future manufacturing professionals to meet the requirements of companies.
The MALAMA project explores the possibilities of laser cleaning technology from an economic and environmental point of view, and aims to make the technology available especially for shipbuilding and the packaging industry.
Surface cleaning using a laser is evaluated in the contexts of both shipbuilding and the packaging industry, both of which are associated with significant potential.
The strengths of the blue economy in Satakunta are linked to e.g. to RDI activities related to the maritime industry. Maritime industry and technology contain a lot of blue economy potential. The maritime industry is changing, e.g. through new environmental responsibility goals. In this change process, the key is to strengthen the know-how related to the maritime cluster and Satakunta maritime technology as the basis of blue growth.
Project timeline: 1.5.2023-30.4.2025
Contact: Prof. Antti Salminen
AIIM is funded under the FICORE (Finnish Indian Consortia for Research and Education) network.
The primary objective of this project is to pioneer novel in-situ process-monitoring methodologies by seamlessly integrating acoustic (sound-based) and optical (light-based) sensors, thereby enabling real-time detection and subsequent correction of process anomalies and subsequently develop cutting-edge machine learning algorithms for predictive process anomaly detection and correction. This proactive approach not only mitigates the need for laborious post-printing inspection and qualification but also enhances the overall manufacturing efficiency
Contact: Prof. Ashish Ganvir and Prof. Antti Salminen
CaNaLiS is a business Finland funded multi-partner project developing process monitoring for laser welding technology. At UTU, in this project we are developing novel sensor (vision, thermal, acoustic etc.) methodology to advance laser welding technology.
Contact: Prof. Antti Salimnen